
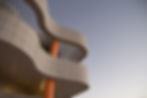

Ultimate Guide to Thin Film Coatings: Deposition and Properties
Overview of Thin Film Coatings
Thin film coatings consist of applying a thin layer (typically a few hundred nanometers or less) of material onto a surface to modify its properties. These coatings are used for different reasons, including protecting the surface, improving its attributes, or changing its optical, electrical, or mechanical characteristics.
Understanding Thin Film Deposition
Various techniques can be used to apply thin films, such as Physical Vapor Deposition, Chemical Vapor Deposition, Dip coating, Spin coating, and Aerosol or ink-jet spray coatings.
Physical Vapor Deposition (PVD)
Thermal Evaporation Process
During thermal evaporation, the substrate to be coated is positioned in a high vacuum chamber or bell jar. Typically, a metal such as aluminum serves as the coating material. The material is loaded into a boat or crucible and heated to its melting point, causing it to vaporize and coat all surfaces within the vacuum chamber that are directly visible. The presence of any shadows created by 3D structures may obstruct a uniform coating on the substrate, necessitating attention. This challenge can be overcome by rotating or moving the substrate within the vacuum chamber relative to the crucible holding the coating material, thereby ensuring an even coating on all surfaces.
Sputtering
Similar to Evaporation, Sputtering is a coating method based on a line-of-sight approach. Rather than melting the coating target, it involves expelling material from the target using high-energy ions such as argon. During this process, inert gas driven by an electric field dislodges atoms from the target, forming a plasma plume of the target material that is subsequently applied to a substrate. Sputtering is effective for coating a variety of materials including glasses, ceramics such as nitrides, carbides, and oxides, non-conductive materials, and specific polymers.
Chemical Vapor Deposition (CVD)
Chemical vapor deposition is a method that does not require direct line of sight and is used to apply a uniform and conformal coating on various surfaces, including sidewalls and hidden features. This process involves filling a vacuum chamber with a chemical vapor precursor, which then evenly covers all areas and breaks down when the substrate is heated above a specific temperature. Therefore, the substrate must be heat-resistant to withstand the high temperatures needed for the precursor to decompose. Materials that can be coated using this method include metals, glasses, oxides, nitrides, carbides, ceramics, and even polymers. However, it should be noted that films produced through this technique may have lower purity levels and potentially higher impurity levels like carbon.
Atmospheric Pressure CVD
Usually, this technique can generate fast film coatings, although the quality may be somewhat lower. The films could experience oxidation and have restricted control over their thickness.
Low Pressure CVD
This encompasses the CVD technique mentioned earlier, but with enhanced precision and regulation of film thickness. Variants comprise:
Plasma Enhanced CVD (PECVD)
Metal Organic CVD (MOCVD)
Modified CVD (employed in the production of fiber optic preforms)
Thermal CVD - traditional chemical vapor deposition
Properties of Thin Film Coatings
Optical Characteristics
The optical characteristics of thin film coatings are largely influenced by the coating method employed. Even sol-gels applied through dipping or spinning processes can yield exceptional optical properties for anti-reflection coatings.
Dielectric mirrors, filters, and anti-reflection coatings of ultra-high quality usually exhibit precision better than 1/10 of a wavelength across the entire surface, contingent upon the initial quality of the substrate surface.
Metalized mirrors can be produced using thermal evaporation or sputtering techniques. These methods are typically carried out in batches, although continuous processing in a reel-to-reel format is also feasible.
Mechanical Properties
The mechanical properties typically vary based on the coating material, application technique, and substrate. These films can reach the highest quality achievable, with the possibility of being grown in single-atom thickness (Atomic Layer Deposition) or as epitaxially oriented films, depending on the substrate and coating materials.
Applications of Thin Film Coatings
Thin films play a crucial role in a wide array of industries and technologies, ranging from Electronics/Semiconductors to Optics, Quantum Devices, MEMS devices, Microfluidics, Embossing/stamping dies, protective films, and many others. In the field of Electronics/Semiconductors, thin films are essential for creating advanced electronic components like transistors, capacitors, and interconnects. These thin films enable the miniaturization of electronic devices, leading to faster and more efficient technology.
Optics heavily depend on thin films for applications such as anti-reflective coatings, optical filters, and mirrors. Thin films in optics are designed to manipulate the behavior of light, allowing for improved performance in various optical systems. Quantum Devices, on the other hand, utilize thin films to control the flow of electrons at the quantum level, enabling the development of quantum computers and other cutting-edge technologies.
MEMS devices (Micro-Electro-Mechanical Systems) rely on thin films for their microscale sensors and actuators. Thin films in MEMS devices enable precise control over mechanical movements and electrical signals, making these devices essential in various industries, including healthcare, automotive, and aerospace.
Microfluidics, a field that deals with the manipulation of fluids at the microscale, heavily utilizes thin films for creating channels, valves, and pumps. Thin film technology in microfluidics enables the development of lab-on-a-chip devices for applications such as medical diagnostics, drug delivery systems, and chemical analysis.
Embossing/stamping dies benefit from thin films for their wear resistance and durability. Thin film coatings on dies protect them from abrasion and extend their lifespan, ensuring consistent and high-quality production in industries like manufacturing and packaging.
Protective films, including coatings for corrosion protection, scratch resistance, and thermal insulation, rely on thin films to enhance the performance and longevity of various materials and surfaces. These protective films play a vital role in preserving the integrity of products in industries such as automotive, aerospace, and construction.
In conclusion, thin films are indispensable in a wide range of fields and technologies, providing unique properties and functionalities that drive innovation and advancement in modern industries.
Optics and Optoelectronics
Thin film coatings play a crucial role in enhancing the performance of various optical components by altering their optical properties. These coatings are commonly used in a wide range of applications such as anti-reflective (AR) coatings, filters, mirrors, and polarizers. In the case of AR coatings, thin film layers are applied to reduce reflections and increase light transmission, thereby improving the overall efficiency of optical systems. Filters rely on thin film coatings to selectively transmit or reflect specific wavelengths of light, enabling applications in areas such as photography, spectroscopy, and telecommunications.
Mirrors benefit from thin film coatings to enhance reflectivity and durability, making them suitable for applications in laser systems, telescopes, and optical instruments. Thin film polarizers are designed to selectively transmit light waves based on their polarization state, allowing for precise control over light polarization in various optical setups. These applications highlight the versatility and importance of thin film coatings in modern optical technology, where their precise design and deposition processes are essential for achieving desired optical performance characteristics.
Semiconductor Devices
Thin-film coatings play a crucial role in the semiconductor industry, particularly on silicon or other semiconducting wafers. These coatings are indispensable for the manufacturing of semiconductors, transistors, and integrated circuits, as they provide essential functionalities and properties to these electronic components. Different types of thin-film coatings are utilized to enhance the performance, durability, and efficiency of the semiconductor devices.
One of the key functions of thin-film coatings is to protect the underlying semiconductor material from environmental factors such as moisture, dust, and chemical contaminants. By acting as a barrier, these coatings help to ensure the reliability and longevity of the electronic devices. Additionally, thin-film coatings can also improve the electrical properties of the semiconductors, such as conductivity, resistance, and capacitance, which are vital for their proper functioning.
Furthermore, thin-film coatings can be engineered to provide specific optical properties, such as anti-reflective coatings or coatings that enhance light absorption. These optical enhancements are crucial for applications in photovoltaics, optical sensors, and display technologies. By tailoring the thickness and composition of the coatings, manufacturers can achieve desired optical effects that optimize the performance of the semiconductor devices.
In conclusion, the use of various types of thin-film coatings on semiconducting wafers is essential for the production of advanced electronic components. These coatings not only protect the semiconductor materials but also enhance their functionality and performance, making them indispensable in the modern semiconductor industry.
Importance of Thin Film Coatings
Thin films play a crucial role in modern technology, serving as a fundamental building block in various industries. These ultra-thin layers of material are essential for the functionality and performance of a wide range of electronic devices, optical components, and even everyday products. The versatility of thin films lies in their ability to modify and enhance the properties of surfaces, such as providing protection against corrosion, improving conductivity, or altering optical characteristics.
In the realm of electronics, thin films are utilized in the production of semiconductors, solar cells, and displays. They enable the miniaturization of electronic components, leading to the development of smaller, faster, and more energy-efficient devices. Thin films are also integral in the manufacturing of sensors, where their thinness allows for increased sensitivity and accuracy in detecting various parameters.
Moreover, in the field of optics, thin films are employed to manipulate the transmission, reflection, and absorption of light. By carefully engineering the thickness and composition of these films, researchers and engineers can create coatings that enhance the performance of lenses, filters, and mirrors. Thin films are also crucial in the development of anti-reflective coatings, which are commonly used in eyeglasses, camera lenses, and architectural glass to reduce glare and improve visibility.
Beyond electronics and optics, thin films find applications in numerous other sectors, including aerospace, automotive, healthcare, and energy. Their ability to provide protective coatings, improve surface properties, and enable novel functionalities makes them indispensable in enhancing the performance and durability of a wide array of products. In essence, the pervasive presence of thin films in our daily lives underscores their significance as a cornerstone of modern technological advancements.
We custom build our own thin film, ultrahigh vacuum deposition systems including:
DC & RF magnetron sputtering ceramics, metal oxides, polymers, glasses, and metals
thermal evaporation - metals
Chemical vapor deposition - nitrides, oxides, and carbides
Pulsed Laser deposition - polymers, ceramics, glasses and metals

Call Ceratek today if you need custom bespoke thin films deposited on
Glasses
Ceramics
Carbides
Semiconductors
Polymers
Virtually anything!
Let us develop your process, and then build you a custom vacuum deposition system