
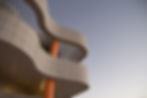

Robotic Laser Welding for Medical Devices: Creating Hermetic Seals
Introduction to Robotic Laser Welding
Robotic laser welding is a cutting-edge technology that combines the precision of robotics with the efficiency of laser welding. This innovative process involves using robotic arms to manipulate a laser beam with extreme accuracy, allowing for the creation of high-quality welds in a wide range of materials. One of the key advantages of robotic laser welding is its ability to produce welds with minimal heat input, which helps prevent distortion and damage to the surrounding material.
Furthermore, robotic laser welding offers unmatched speed and consistency compared to traditional welding methods. The automated nature of the process ensures that welds are uniform and repeatable, leading to improved overall quality and productivity. Additionally, the flexibility of robotic arms allows for welding in complex geometries and hard-to-reach areas, making it ideal for a variety of industries such as automotive, aerospace, and electronics.
Overall, robotic laser welding represents a cutting-edge solution for manufacturers looking to enhance their welding processes through advanced technology. By combining the precision of robotics with the efficiency of laser welding, this innovative approach offers numerous benefits in terms of quality, speed, and versatility.
The Significance of Hermetic Sealing in Medical Devices
Hermetic sealing plays a crucial role in ensuring the integrity and reliability of medical devices. This specialized sealing method involves creating a completely airtight and watertight seal around sensitive components within the device. By achieving hermetic sealing, medical devices can be protected from external elements such as moisture, gases, and contaminants that could compromise their functionality or pose risks to patients.
One of the key benefits of hermetic sealing in medical devices is its ability to prevent the ingress of fluids and bacteria, which is essential for devices that come into contact with bodily fluids or tissues. This barrier helps maintain the sterility of the device and reduces the risk of infections or other complications during medical procedures.
Furthermore, hermetic sealing also contributes to the longevity and durability of medical devices by shielding internal components from corrosion and degradation. This is particularly important for implantable devices that need to function reliably within the body for extended periods.
Overall, the meticulous process of hermetic sealing in medical devices underscores the importance of quality assurance and regulatory compliance in the healthcare industry. By upholding strict standards for sealing integrity, manufacturers can ensure the safety and effectiveness of medical devices, ultimately benefiting patients and healthcare providers alike.
Importance of Hermetic Seals
Hermetic seals play a crucial role in various industries and applications where maintaining airtight and leak-proof environments is essential. These seals are designed to prevent the ingress of moisture, gases, or other contaminants into sensitive components or systems, ensuring their integrity and functionality. In industries such as aerospace, automotive, electronics, and healthcare, hermetic seals are used to protect delicate instruments, electronic circuits, sensors, and other critical components from environmental factors that could compromise their performance.
In medical devices and pharmaceutical applications, hermetic seals are **crucial** for ensuring the sterility and reliability of implants, instruments, and drug delivery systems.
Challenges in Hermetic Sealing
Hermetic sealing poses a range of challenges that must be carefully addressed to ensure the integrity and reliability of the sealed system. One of the primary challenges in hermetic sealing is achieving a completely air-tight seal that prevents any gases or liquids from entering or escaping the sealed environment. This requires precise engineering and manufacturing processes to eliminate any potential leakage paths, such as gaps or imperfections in the sealing materials.
Furthermore, the materials used for hermetic sealing must be carefully selected to withstand the specific environmental conditions to which the sealed system will be exposed. Factors such as temperature fluctuations, pressure differentials, and exposure to corrosive substances can all impact the performance of the seal over time. Selecting the appropriate materials with the right properties, such as thermal expansion coefficients and chemical resistance, is crucial to ensuring the long-term effectiveness of the hermetic seal.
Another challenge in hermetic sealing is maintaining the integrity of the seal during the operational life of the system. Mechanical stresses, vibration, and other external forces can put strain on the seal, potentially compromising its effectiveness over time. Design considerations, such as incorporating flexible elements or protective features, can help mitigate these risks and ensure the seal remains intact under varying conditions.
In addition, testing and quality control are essential aspects of hermetic sealing to verify the effectiveness of the seal and detect any potential issues before they impact the performance of the sealed system. Various testing methods, such as helium leak testing or optical inspection and X-ray, can be employed to assess the quality of the seal and identify any areas for improvement.
Overall, addressing the challenges in hermetic sealing requires a comprehensive approach that encompasses material selection, design considerations, manufacturing processes, testing procedures, and ongoing quality control measures. By carefully considering and managing these challenges, engineers can create reliable hermetic seals that meet the stringent requirements of various applications.
Advantages of Robotic Laser Welding in Medical Device Manufacturing
Robotic laser welding in medical device manufacturing offers a myriad of advantages that significantly contribute to the overall efficiency and quality of the production process. One of the key benefits is the precision and accuracy achieved through the use of robotic systems, which ensures consistent and high-quality welds, critical for medical devices where precision is paramount. Additionally, robotic laser welding allows for increased automation and repeatability, reducing the margin of error and enhancing the overall reliability of the manufacturing process.
Moreover, the use of robotic systems in laser welding enables manufacturers to improve productivity by speeding up the welding process and increasing throughput. This not only leads to cost savings but also allows for faster turnaround times, which is crucial in the medical device industry where timely production is essential. Furthermore, robotic laser welding offers a high degree of flexibility, allowing for the welding of complex geometries and intricate designs with ease, which may be challenging to achieve with traditional welding methods.
Another significant advantage of robotic laser welding in medical device manufacturing is the ability to work with a wide range of materials, including stainless steel, titanium, and various alloys commonly used in medical device fabrication. This versatility makes robotic laser welding a versatile and adaptable solution for meeting the diverse needs of the medical industry.
Overall, the adoption of robotic laser welding in medical device manufacturing brings numerous benefits, including improved precision, efficiency, productivity, and material compatibility. By harnessing the power of robotic systems, manufacturers can elevate the quality of their products while streamlining their production processes to meet the stringent requirements of the medical device industry.
Robotic Welding Technology for Hermetic Sealing
Robotic welding technology for hermetic sealing is a cutting-edge method that combines the precision of robotics with the efficiency of laser or inert gas welding to create airtight seals in various applications. This advanced technology utilizes robotic arms equipped with welding tools to perform intricate welding tasks with unmatched accuracy and speed, ensuring the creation of hermetically sealed joints that are crucial in industries such as automotive, aerospace, and electronics.
The process involves programming the robotic system to follow specific welding paths and parameters, guaranteeing consistent and reliable results. By leveraging robotic welding technology for hermetic sealing, manufacturers can achieve high levels of repeatability and quality in their production processes. This not only enhances the overall product quality but also increases productivity by reducing manual labor and minimizing the risk of errors.
Furthermore, robotic welding technology offers a high degree of flexibility, allowing for the customization of welding patterns and techniques to suit the unique requirements of each application. This adaptability makes it an ideal solution for a wide range of hermetic sealing tasks, from sealing electronic components to joining metal parts in critical assemblies.
In conclusion, robotic welding technology for hermetic sealing represents a significant advancement in manufacturing processes, offering unparalleled precision, efficiency, and reliability. By harnessing the power of robotics in welding applications, industries can elevate their production capabilities and meet the demanding standards of modern manufacturing with ease. Most importantly is the repeatability of the process!
Applications of Robotic Laser Welding in Medical Devices
Robotic laser welding has revolutionized the manufacturing processes in the medical devices industry. The precision and accuracy offered by robotic systems have made them an indispensable tool in creating intricate and delicate medical devices. One of the key applications of robotic laser welding in this field is the assembly of components with high precision requirements, such as catheters, surgical instruments, and implantable devices.
The ability of robotic systems to perform welds in difficult-to-reach areas with minimal human intervention ensures the quality and consistency of the welds, which is crucial for the safety and effectiveness of medical devices. Moreover, robotic laser welding allows for the joining of dissimilar materials, enabling the production of devices with unique material properties tailored to specific medical applications.
Another significant advantage of robotic laser welding in the medical devices industry is its ability to work with a wide range of materials, including stainless steel, titanium, and various biocompatible alloys. This versatility makes robotic laser welding suitable for a diverse array of medical device applications, from orthopedic implants to diagnostic tools.
Furthermore, robotic laser welding offers increased efficiency and cost-effectiveness in the manufacturing process of medical devices. The automation of welding tasks reduces the risk of human error and ensures a higher level of repeatability, leading to improved product quality and consistency. This, in turn, results in reduced scrap rates and rework, ultimately lowering production costs and increasing overall productivity.
In conclusion, the applications of robotic laser welding in the medical devices industry are vast and varied, ranging from intricate component assembly to the joining of dissimilar materials. The precision, versatility, efficiency, and cost-effectiveness of robotic laser welding make it an indispensable technology in the manufacturing of high-quality and reliable medical devices that are essential for improving patient care and outcomes.
Best Practices for Robotic Laser Welding in Medical Device Production
When it comes to robotic laser welding in medical device production, following best practices is crucial to ensure efficiency, precision, and quality in the manufacturing process. Utilizing advanced robotics equipped with laser technology allows for intricate welding tasks to be performed with high accuracy and repeatability.
One of the key best practices is to carefully calibrate the robotic welding system to optimize parameters such as laser power, welding speed, and focal length. This calibration process ensures that the welds are consistent and meet the required quality standards. Additionally, implementing a thorough quality control system that includes regular inspections and testing of the welds is essential to identify any defects early on and prevent faulty products from reaching the market.
Furthermore, proper maintenance of the robotic welding equipment is essential to prolong its lifespan and ensure optimal performance. This includes regular cleaning, lubrication, and inspection of components to prevent breakdowns and minimize downtime. Training operators and technicians on the correct operation and maintenance procedures is also crucial to maximize efficiency and safety in the production environment. Having good documentation, Work Instructions, an IQ/OQ/PQ evaluation plan and Site Acceptance conformance is key to a quality managed process.
Incorporating these best practices into the robotic laser welding process for medical device production not only enhances productivity and quality but also contributes to overall cost savings and customer satisfaction. By prioritizing precision, consistency, and adherence to industry standards, manufacturers can achieve superior results in the production of critical medical devices.
If your project needs precision hermetic welding, tabbing or general laser welding, let us know how we can help! Call or email Ceratek today for a quote.